آشنایی با برش لیزر
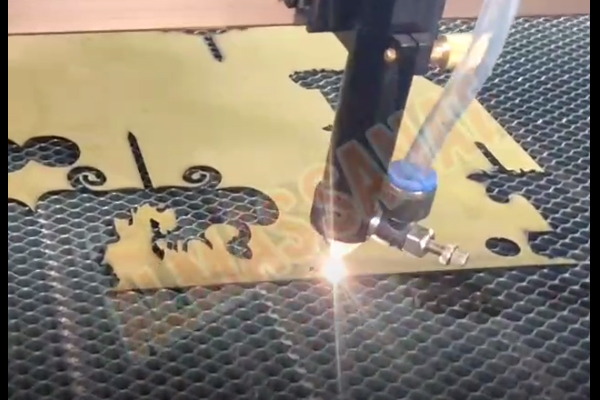
آشنایی با برش لیزر
برش لیزری یک فرآیند ساخت است که از یک پرتو لیزر متمرکز و پرقدرت برای برش مواد به اشکال و طرح های سفارشی استفاده می کند. این فرآیند برای طیف وسیعی از مواد از جمله فلز، پلاستیک، چوب، سنگهای قیمتی، شیشه و کاغذ مناسب است و میتواند قطعات دقیق و پیچیدهای را تولید کند.
انواع مختلفی از برش لیزری موجود است، از جمله برش فیوژن، برش اکسیداسیون و خراش دادن. هر فرآیند برش لیزری میتواند برش قطعات را با دقت و کیفیت بالاتولید کند. و به طور کلی با آلودگی كمتر، آسیب فیزیکی و ضایعات کمتر نسبت به سایر فرآیندهای برش معمولی مانند برش مکانیکی و برش واترجت. در حالی که برش لیزری مزایای خاصی را نسبت به فرآیندهای برش معمولی نشان می دهد، ولي در برخی از کاربردهای تولیدی می تواند مشکل ساز باشد، مانند برش مواد بازتابنده یا موادی که نیاز به ماشینکاری و تکمیل کار ثانویه دارند.
هر فرآیند برش، مزایا و معایب خود را دارد، این مقاله بر برش لیزری تمرکز دارد و اصول اولیه این فرآیند و اجزاء و مکانیک لازم دستگاه برش لیزر را بیان میکند. علاوه بر این، این مقاله به بررسی روشها و کاربردهای مختلف برش لیزری، مزایا و محدودیتهای فرآیند، و مقایسه بین برش لیزری و انواع دیگر فرآیندهای برش میپردازد.
دستگاه و فرآیند برش لیزری
برش لیزری یک فرآیند ساخت غیر تماسی و مبتنی بر حرارت است که برای مواد فلزی و غیرفلزی مناسب است. برای اینکه این فرآیند بدون مشکل و با ظرفیت بهینه اجرا شود، عوامل مختلفی باید در نظر گرفته شود، مانند پیکربندی و تنظیمات دستگاه برش لیزر
بررسی اجمالی اجزاء و مکانیک دستگاه لیزر
بر خلاف برش مکانیکی، که از ابزارهای برش و تجهیزات برقی استفاده می کند. و برش واترجت، که از آب تحت فشار و مواد ساینده استفاده می کند. برش لیزری از یک دستگاه برش لیزری برای تولید برش، حکاکی و علامت گذاری استفاده می کند. در حالی که ماشینهای برش لیزری از مدلی به مدل دیگر و کاربرد به کاربرد متفاوت هستند، فرآیند اصلی آنها شامل مراحل زیر است:
- تولید پرتو
- تمرکز پرتو
- گرمایش و ذوب موضعی
- بیرون ریختن مواد
- حرکت پرتو
هر مرحله از فرآیند برش لیزری اجتناب ناپذیر است و وقتی به درستی اجرا شود، یک برش دقیق ایجاد می کند.
توليد پرتو :
واژه لیزر از مخفف LASER یا Light Amplification by Stimulated Emission of Radiation گرفته شده است. در اصل، این مخفف اصول اولیه تولید لیزر – تحریک و تقویت را خلاصه می کند. همراه با این اصول، تشدید کننده لیزر از فرآیندهای گسیل خود به خود و انتشار تحریک شده برای تولید یک پرتو نور با شدت بالا استفاده می کند که هم از نظر فضایی و هم از نظر طیفی منسجم است (یعنی یک پرتو لیزر).
*انتشار خود به خود:
تشدید کننده لیزر حاوی یک محیط لیزر فعال (مانند CO2) است که الکترون های آن توسط یک منبع انرژی خارجی، مانند لامپ فلاش یا قوس الکتریکی تحریک می شوند. همانطور که محیط انرژی دریافت و جذب می کند، اتم های آن فرآیندی را تجربه می کنند که به عنوان انتشار خود به خود شناخته می شود. در طی این فرآیند، انرژی جذب شده توسط یک اتم باعث می شود که الکترون های اتم برای مدت کوتاهی به سطح انرژی بالاتری بپرند و سپس به حالت اولیه خود بازگردند. پس از بازگشت الکترون ها به حالت پایه خود، اتم فوتون نوری ساطع می کند.
*گسیل تحریک شده:
فوتون هایی که توسط گسیل خود به خودی تولید می شوند در محیطی حرکت می کنند که در حفره تشدیدگر لیزری بین دو آینه قرار دارد. یک آینه بازتابنده است تا فوتون ها را در محیط حرکت دهد، بنابراین آنها به انتشار گسیل های تحریک شده ادامه می دهند، و آینه دیگر تا حدی انتقال دهنده است تا به برخی فوتون ها اجازه فرار بدهد. گسیل تحریکشده فرآیندی است که در آن یک فوتون (یعنی فوتون فرودی) اتمی را تحریک میکند که از قبل در سطح انرژی بالاتری قرار دارد. این برهمکنش اتم تحریک شده را مجبور می کند تا با گسیل یک فوتون دوم با همان طول موج ثابت با فوتون فرود، به حالت پایه خود بیفتد.
فرآیند انتشار یک فوتون، گسیل فوتون دیگر، قدرت و شدت پرتو نور را تقویت می کند. بنابراین انتشار تحریک شده فوتون های نور (یعنی نوعی تابش الکترومغناطیسی) باعث تقویت نور می شود. به عبارت دیگر، تقویت نور با انتشار تحریک شده تابش. فوتون های نادرست در رزوناتور از طریق آینه نیمه انتقال دهنده بدون انعکاس به محیط عبور می کنند و پرتو لیزر اولیه را ایجاد می کنند. پس از تولید، پرتو وارد سر برش لیزر شده و توسط آینه ها به عدسی فوکوس هدایت می شود.
تمركز پرتو
لنز فوکوس پرتو لیزر را از طریق مرکز نازل در انتهای سر برش لیزر که برخورد می کند به سطح قطعه کار متمرکز می کند. با فوکوس کردن پرتو، عدسی انرژی پرتو را در نقطه کوچکتری متمرکز می کند که شدت پرتو را افزایش می دهد. معادله زیر اصل اساسی پشت این اتفاق را نشان می دهد:
جایی که P نشان دهنده قدرت پرتو لیزر اولیه و πr2 نشان دهنده سطح مقطع پرتو است. همانطور که لنز پرتو لیزر را متمرکز می کند، شعاع rپرتو کاهش می یابد. این کاهش شعاع، سطح مقطع را کاهش می دهد، که به نوبه خود شدت آن را افزایش می دهد زیرا اکنون قدرت آن در سطح کوچکتری توزیع می شود.
گرمایش و ذوب موضعی و خروج مواد
همانطور که پرتو به سطح ماده برخورد می کند، مواد تشعشع را جذب می کند و انرژی داخلی را افزایش می دهد و گرما تولید می کند. شدت بالای پرتو لیزر به آن اجازه می دهد تا یک ناحیه موضعی از سطح قطعه کار را گرم، ذوب و تا حدی یا به طور کامل تبخیر کند. ضعیف شدن و حذف ناحیه آسیب دیده مواد، برش های مورد نظر را تشکیل می دهد. برش لیزری از چندین نوع مکانیزم برش و حذف مواد استفاده می کند، از جمله برش ذوبی، برش تخریب شیمیایی، برش تبخیر، خط کشی و برش اکسیداسیون.
– برش فیوژن:
که به آن برش مذاب گاز بی اثر یا برش گاز بی اثر نیز گفته می شود، برش فیوژن توسط دستگاه های برش لیزر CO2 استفاده می شود. پرتو لیزر تولید شده توسط دستگاه برش قطعه کار را ذوب می کند و مواد ذوب شده توسط یک جت گاز کمکی به کار رفته از ته قفسه خارج می شود. گاز کمکی و فشار گاز کمکی به کار گرفته شده به نوع ماده بریده شده بستگی دارد، اما گاز بی اثر همیشه بر اساس عدم واکنش شیمیایی آن نسبت به ماده انتخاب می شود. این مکانیزم برای برش اکثر فلزات و ترموپلاستیک ها مناسب است.
– تخریب شیمیایی:
تجزیه شیمیایی توسط دستگاه های برش لیزر CO2 استفاده می شود و برای برش لیزری پلیمرهای گرماسخت و مواد آلی مانند چوب مناسب است. از آنجایی که مواد ترموست و آلی در هنگام اعمال گرما ذوب نمی شوند، پرتو لیزر در عوض مواد را می سوزاند و به کربن و دود تبدیل می کند.
– برش تبخیری:
برش تبخیری توسط دستگاه های برش لیزر CO2 استفاده می شود و به دلیل نزدیک بودن نقطه ذوب و جوش برای موادی مانند اکریلیک و پلی استال برش لیزری مناسب است. از آنجایی که لیزر تبخیر مواد در طول برش تبخیر می شود، لبه تولید شده به طور کلی براق و صیقلی است.
– خط كشي:
خط کشی توسط دستگاه های برش لیزر CO2 و Nd:YAG برای ایجاد شیارها یا سوراخ هایی با نفوذ جزئی یا کامل، معمولاً بر روی سرامیک ها یا تراشه های سیلیکونی استفاده می شود. این شیارها و سوراخ ها امکان شکستن مکانیکی در امتداد خطوط ساختاری ضعیف شده را فراهم می کنند.
– برش اکسیداسیون:
که به آن برش اکسیژن شعله نیز گفته می شود، برش اکسیداسیون توسط دستگاه های برش لیزر CO2 و Nd:YAG استفاده می شود و برای برش لیزری فولادهای نرم و کربنی مناسب است. برش اکسیداسیون یکی از نمونههای مکانیزم برش مذاب گاز راکتیو است که به طور خاص از گازهای کمکی واکنشپذیر شیمیایی استفاده میکند. همانطور که از نامش پیداست، برش اکسیداسیون از اکسیژن به عنوان گاز کمکی استفاده می کند که به طور گرمازایی با مواد واکنش می دهد. گرمای تولید شده فرآیند برش را تسریع میکند. یک لبه مذاب اکسید شده تولید میکند. که میتواند به راحتی توسط یک جت گاز حذف شود تا لبه تمیزتر ایجاد شود.
حرکت پرتو
هنگامی که گرمایش موضعی، ذوب یا تبخیر شروع شد، دستگاه ناحیه حذف مواد را در سراسر قطعه کار حرکت می دهد تا برش کامل ایجاد شود. این دستگاه با تنظیم آینه های بازتابنده، کنترل سر برش لیزری یا دستکاری قطعه کار به حرکت دست می یابد. سه پیکربندی مختلف برای ماشینهای برش لیزری وجود دارد که با نحوه حرکت یا حرکت پرتو لیزر بر روی مواد تعریف میشوند: مواد متحرک، Flying Optics ، و سیستمهای برش لیزر ترکیبی.-
*مواد متحرک:
دستگاه های برش لیزری مواد متحرک، دارای یک پرتو لیزر ثابت و یک سطح برش متحرک هستند که مواد به آن چسبانده می شود. قطعه کار به صورت مکانیکی در اطراف تیر ثابت حرکت می کند تا برش های لازم ایجاد شود. این پیکربندی اجازه می دهد تا فاصله ایستادن یکنواخت و ثابتی داشته باشد و به اجزای نوری کمتری نیاز دارد.
*Flying Optics :
دستگاه های برش لیزری Flying Optics دارای یک سرمتحرک و یک قطعه کار ثابت هستند. سر برش تیر را روی قطعه کار ثابت در محورهای X و Y حرکت می دهد تا برش های لازم را ایجاد کند. انعطافپذیری دستگاههای اپتیک پرنده برای برش مواد با ضخامت و اندازههای متغیر و همچنین زمانهای پردازش سریعتر مناسب است. با این حال، از آنجایی که پرتو به طور مداوم در حال حرکت است، طول پرتو در حال تغییر باید در طول فرآیند در نظر گرفته شود. طول پرتو در حال تغییر را می توان با کولیماسیون (هم ترازی اپتیک)، با استفاده از یک محور طول پرتو ثابت، یا استفاده از اپتیک تطبیقی یا سیستم کنترل ارتفاع خازنی که قادر به انجام تنظیمات لازم در زمان واقعی است، کنترل کرد.
*دستگاه های برش لیزری ترکیبی:
ترکیبی از ویژگی های موجود در مواد متحرک و دستگاه های اپتیک پرنده را ارائه می دهند. این ماشینها دارای یک میز جابجایی مواد هستند که روی یک محور (معمولاً محور X) حرکت میکند و یک سر لیزری که روی محور دیگری (معمولاً محور Y) حرکت میکند. سیستمهای هیبریدی در مقایسه با سیستمهای اپتیک پرنده، امکان تحویل پرتوهای سازگارتر و کاهش تلفات توان و ظرفیت بیشتر در هر وات را فراهم میکنند.
لیزرها به صورت پرتوهای پالسی یا پرتوهای موج پیوسته تولید می شوند. مناسب بودن هر کدام به خواص ماده برش داده شده و نیازهای کاربردهای برش لیزری بستگی دارد. پرتوهای پالسی به صورت انفجارهای کوتاه خروجی توان تولید می شوند. در حالی که پرتوهای موج پیوسته به صورت خروجی توان بالا و پیوسته تولید می شوند. نوع اولی معمولاً برای برنامه های برش خط یا تبخیر استفاده می شود و برای برش طرح های ظریف یا سوراخ کردن مواد ضخیم مناسب است، در حالی که دومی برای برنامه های برش با راندمان بالا و سرعت بالا مناسب است.
انواع گازهای کمکی
برش لیزری از انواع گازهای کمکی برای کمک به فرآیند برش استفاده می کند. فرآیند برش به کار گرفته شده و مواد برش داده شده، تعیین کننده نوع گاز کمکی – چه بی اثر یا فعال – است که برای استفاده مناسب است.
– برش گاز بی اثر
(به عنوان مثال، برش ذوب یا برش مذاب گاز بی اثر)، همانطور که در نام مشخص است، از گازهای کمکی بی اثر شیمیایی استفاده می کند. گاز کمکی خاص مورد استفاده به خواص واکنشی ماده بستگی دارد. به عنوان مثال، از آنجایی که ترموپلاستیک های مذاب با نیتروژن و اکسیژن واکنش نمی دهند، هوای فشرده می تواند به عنوان گاز کمکی هنگام برش چنین موادی استفاده شود. از سوی دیگر، از آنجایی که تیتانیوم مذاب با نیتروژن و اکسیژن واکنش می دهد، آرگون – یا گاز بی اثر شیمیایی مشابه دیگری – باید به عنوان گاز کمکی در کاربردهای برش لیزری که شامل این ماده است استفاده شود. هنگام برش فولاد ضد زنگ از طریق فرآیند برش گاز بی اثر، نیتروژن معمولاً به عنوان گاز کمکی استفاده می شود. این به این دلیل است که فولاد ضد زنگ مذاب با اکسیژن واکنش شیمیایی می دهد.
– برش گاز فعال
هنگامی که مواد برش لیزری از طریق فرآیند برش مذاب واکنشی، یک گاز کمک فعال (یعنی واکنش شیمیایی) – معمولاً اکسیژن – برای تسریع فرآیند برش استفاده می شود. در حالی که در برش گاز بی اثر، مواد تنها با قدرت لیزر گرم، ذوب و تبخیر می شوند، در برش گاز راکتیو واکنش بین گاز کمکی و ماده باعث ایجاد گرمای اضافی می شود که به فرآیند برش کمک می کند. به دلیل این واکنش گرمازا، برش گاز راکتیو معمولاً به سطوح توان لیزر کمتری برای برش مواد در مقایسه با سطح توان لازم هنگام برش مواد مشابه از طریق فرآیند برش گاز بی اثر نیاز دارد.
فشار برش گاز کمکی مورد استفاده نیز با فرآیند برش به کار رفته و خواص و ضخامت ماده برششده تعیین میشود. به عنوان مثال، پلیمرها معمولاً به فشار جت گاز 2-6 بار در طول فرآیند برش گاز بی اثر نیاز دارند. در حالی که فولاد ضد زنگ به فشار جت گاز 8-14 بار نیاز دارد. بر این اساس، مواد نازکتر نیز عموماً به فشار کمتری نیاز دارند و مواد ضخیمتر معمولاً به فشار بیشتری نیاز دارند. در برش اکسیداسیون برعکس این موضوع صادق است.یعنی هر چه ماده ضخیم تر باشد، فشار مورد نیاز کمتر می شود. هر چه ماده نازک تر باشد، فشار مورد نیاز بیشتر می شود.
انواع دستگاه های برش لیزری
انواع مختلفی از دستگاه های برش موجود است که به لیزرهای گازی، مایع و جامد دسته بندی می شوند. که بر اساس وضعیت محیط لیزر فعال – یعنی اینکه آیا این محیط یک ماده گاز، مایع یا جامد است – و اینکه محیط لیزر فعال از چه چیزی تشکیل شده است (به عنوان مثال CO2، Nd:YAG و غیره) متمایز می شوند. دو نوع اصلی لیزرهای مورد استفاده عبارتند از CO2 و لیزرهای حالت جامد.
1- ليزرهاي گازي:
یکی از رایج ترین لیزرهای حالت گازی، لیزر CO2 از مخلوط دی اکسید کربن به عنوان محیط لیزر فعال استفاده می کند. لیزرهای CO2 معمولاً برای برش مواد غیر فلزی استفاده میشوند زیرا مدلهای اولیه به اندازه کافی برای برش فلزات قدرتمند نبودند. فناوری لیزر از آن زمان به گونه ای تکامل یافته است که لیزرهای CO2 را قادر می سازد تا فلزات را برش دهند، اما لیزرهای CO2 هنوز برای برش از طریق غیر فلزات و مواد آلی (مانند لاستیک، چرم، یا چوب) و به سادگی حکاکی فلزات یا سایر مواد سخت مناسب تر هستند. لیزرهای نیتروژن خالص یکی دیگر از لیزرهای رایج حالت گازی هستند. این لیزرها برای کاربردهایی استفاده میشوند که نیاز به اکسید شدن مواد در هنگام برش دارند.
2- ليزرهاي حالت جامد:
انواع مختلفی از لیزرهای حالت جامد در دسترس هستند، از جمله لیزرهای کریستال و فیبر. لیزرهای کریستالی از انواع محیطهای کریستالی مانند گارنت آلومینیوم ایتریوم دوپ شده با نئودیمیم (Nd:YAG) یا ارتووانادات ایتریم دوپ شده با نئودیمیم (Nd:YVO4) استفاده میکنند. که امکان برش لیزری فلزات و غیرفلزی با قدرت بالا را فراهم میکنند. اگرچه لیزرهای کریستال از نظر قابلیت های برش مواد همه کاره هستند، اما معمولاً لیزرهای کریستال گران تر هستند. و طول عمر کمتری نسبت به انواع دیگر لیزرها دارند. لیزرهای فیبر جایگزین ارزانتر و ماندگارتري برای لیزرهای کریستالی هستند. این نوع لیزر ابتدا یک پرتو از طریق یک سری دیود لیزر ایجاد می کند که سپس از طریق فیبرهای نوری كه منتقل می شود، تقویت می شود و بر روی قطعه کار متمرکز می شود تا برش های لازم را انجام دهد.
ملاحظات دستگاه برش لیزری
همانطور که در بخش قبل توضیح داده شد، نوع لیزر مناسب برای کاربرد برش لیزر تا حد زیادی با مواد برش داده شده تعیین می شود. با این حال، ملاحظات دیگری ممکن است در هنگام انتخاب و راهاندازی دستگاه در نظر گرفته شود. برای یک کاربرد خاص، مانند پیکربندی دستگاه، توان لیزر، طول موج، حالت زمانی، حالت مکانی و اندازه نقطه کانونی.
توان لیزر:
توان لیزر یا وات می تواند کل زمان پردازش را برای یک برنامه برش افزایش یا کاهش دهد. این اتفاق به دلیل افزایش شدت پرتو با افزایش توان لیزر است (چگالی توان (Intensity) = P/πr2). قیمت دستگاه معمولاً به قدرت لیزر بستگی دارد. هرچه لیزر قوی تر باشد، تجهیزات گران تر است. بنابراین تولیدکنندگان و کارگاهها هنگام انتخاب دستگاه لیزر بر اساس توان لیزر، باید تعادلی بین هزینههای پردازش و هزینههای تجهیزات پیدا کنند.
طول موج:
طول موج پرتو لیزر، طول فضایی یک چرخه کامل ارتعاش برای فوتون درون پرتو است. و تا حدی میزان جذب تشعشع ماده را تعیین میکند، که به ماده اجازه میدهد تا گرم، ذوب و تبخیر شود تا برشهای لازم را ایجاد کند.
حالت پرتو:
حالت به نحوه توزیع شدت پرتو لیزر در سطح مقطع پرتو اشاره دارد. این حالت بر اندازه نقطه کانونی پرتو و شدت پرتو تأثیر می گذارد که به نوبه خود بر کیفیت برش تأثیر می گذارد. به طور معمول، حالت بهینه دارای یک توزیع شدت (TEM00) است.
نقطه کانونی:
پرتو از طریق یک عدسی یا یک آینه تخصصی هدایت می شود و به نقطه کوچکی با شدت بالا متمرکز می شود. نقطه ای که قطر پرتو در آن کوچکترین است، نقطه کانونی یا کانون نامیده می شود. موقعیت بهینه فوکوس برای کاربرد برش لیزری به عوامل مختلفی بستگی دارد. از جمله خواص و ضخامت ماده، شکل و حالت پرتو، نوع گاز کمکی و وضعیت لنز کانونی.